Introduction
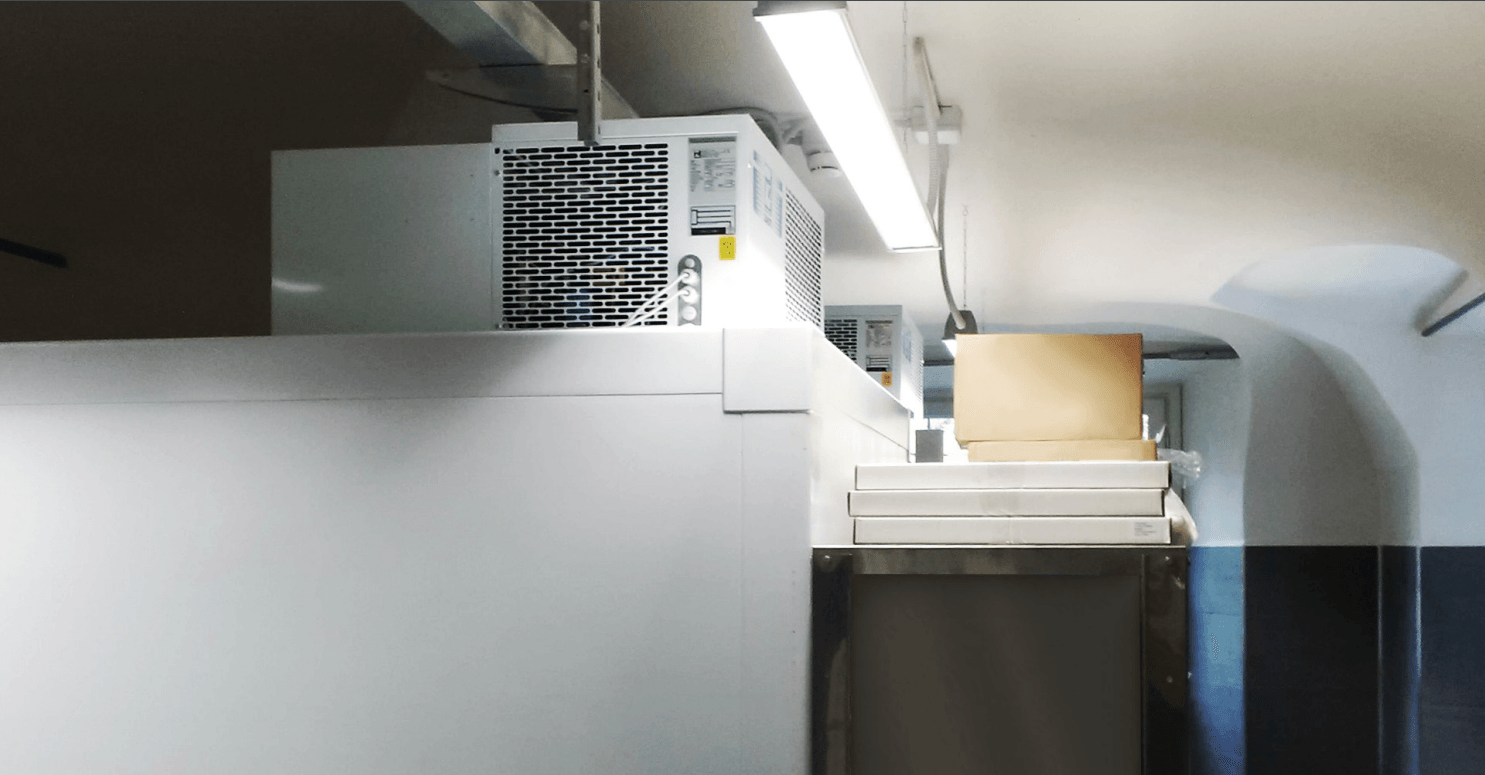
"Arctic Active Cooling. Endless Possibilities. We capture new technologies in mobile and compact cooling. Full-size cooling in a miniature design, customized to make your device stand out with innovative thermal management."
In the realm of industrial operations, the cold room refrigeration system stands as a pivotal component, ensuring that perishable goods maintain their integrity and quality. Whether it’s food storage, pharmaceuticals, or other temperature-sensitive products, these systems play a crucial role in various industries. Understanding the intricacies of cold room components and their applications can provide businesses with a competitive edge in today's market.
The Importance of Cold Room Refrigeration
Cold room refrigeration is essential for preserving the freshness and safety of products across multiple sectors. By regulating temperatures effectively, these systems minimize spoilage and waste, leading to significant cost savings for businesses. Moreover, compliance with health regulations often hinges on the proper use of cold rooms, making them indispensable in food service and medical fields.
Understanding Cold Room Components
To appreciate how a cold room refrigeration system operates, it's vital to grasp its key components—compressors, evaporators, condensers, and thermal insulation all work together seamlessly. Each part serves a specific function that contributes to efficient cooling and energy management within the space. Familiarity with these components not only aids in troubleshooting but also enhances decision-making when selecting equipment for optimal performance.
Industrial Applications of Cold Rooms
The versatility of industrial cold rooms extends to various applications—from storing fresh produce in supermarkets to maintaining pharmaceuticals at precise temperatures in hospitals. These specialized environments cater to industries that require strict temperature controls for product longevity and safety. As businesses increasingly recognize the value of investing in advanced cooling solutions like Arctic Active Cooling's Top-Mounted Monoblock Refrigeration Unit, they are better equipped to meet both operational demands and sustainability goals.
What is a Cold Room Refrigeration System?
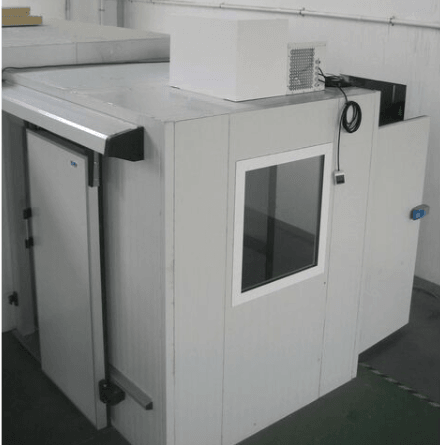
Cold room refrigeration systems are specialized setups designed to maintain low temperatures for various industrial applications. These systems are essential for preserving perishable goods, ensuring product quality, and extending shelf life. By controlling the environment within a cold room, businesses can effectively manage inventory and reduce waste.
Definition and Functionality
A cold room refrigeration system is essentially an enclosed space equipped with cooling technology to maintain specific temperature ranges suitable for storage or processing. The functionality of these systems revolves around the removal of heat from the interior environment, utilizing refrigerants to facilitate this process efficiently. This setup not only preserves temperature-sensitive products but also helps in complying with industry standards regarding food safety and quality.
Key Components of Cold Room Refrigeration
The key components of cold room refrigeration include compressors, condensers, evaporators, and insulation materials that work together harmoniously. Compressors circulate refrigerants through the system while condensers release heat outside the cold room; evaporators absorb heat from inside to maintain low temperatures. Additionally, proper insulation is crucial to minimize energy loss and enhance efficiency across all Coldroom Refrigeration Systems.
Benefits for Industries
Industries benefit immensely from adopting a cold room refrigeration system as it directly impacts their operational efficiency and product integrity. By utilizing these systems, businesses can ensure that perishable items such as food products or pharmaceuticals remain in optimal condition throughout their shelf life. Furthermore, investing in advanced equipment like Arctic Active Cooling's Top-Mounted Monoblock Refrigeration Unit enhances reliability and performance while promoting sustainability—an essential factor for modern enterprises.
Which Refrigerant is Used in Cold Rooms?
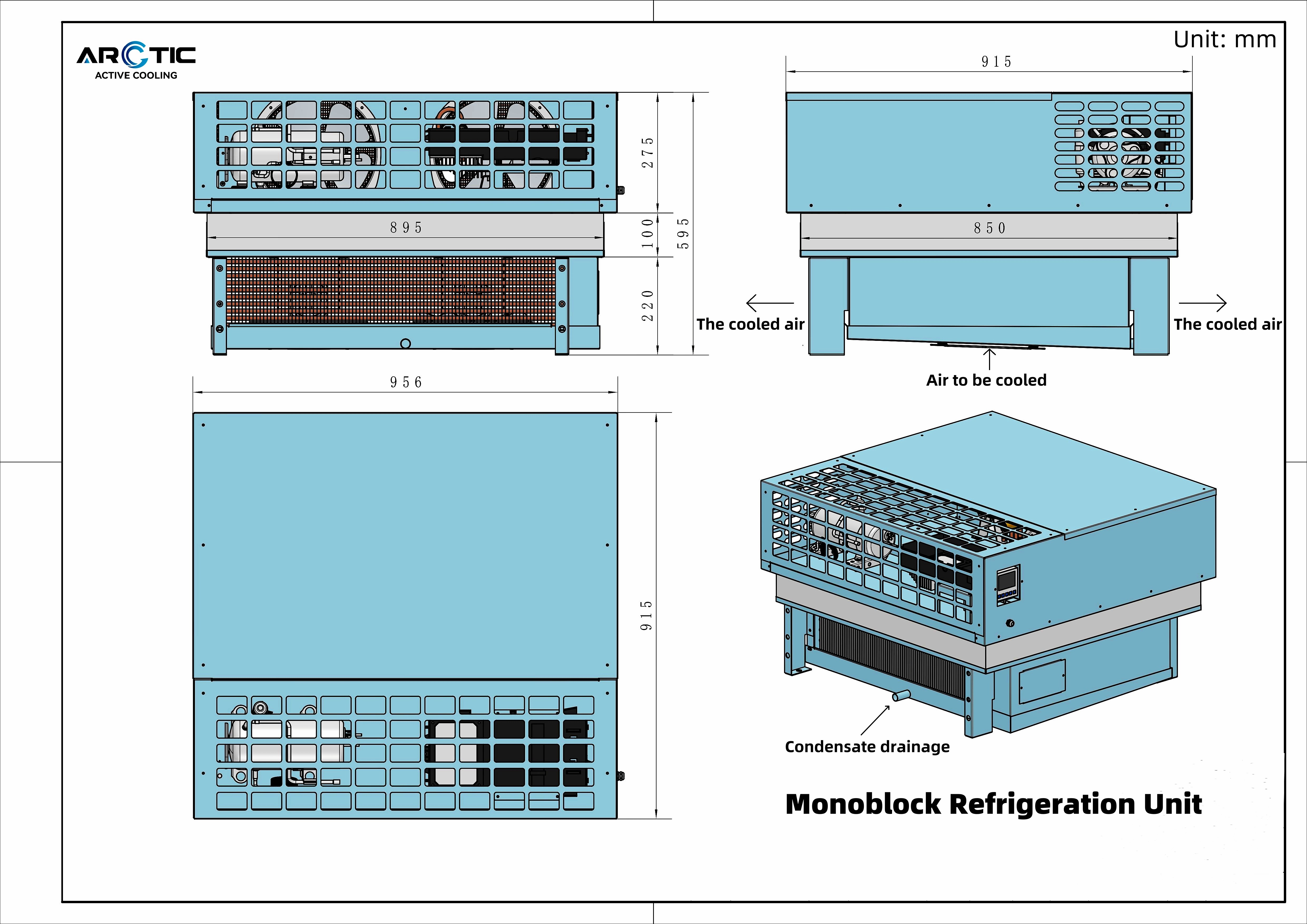
Common Refrigerants in Use
There are several common refrigerants utilized in cold room refrigeration systems, each with its unique properties and applications. Hydrofluorocarbons (HFCs), such as R-134a and R-404A, have been popular due to their effective cooling capabilities. However, some industries are shifting towards natural refrigerants like ammonia (R-717) and carbon dioxide (R-744) for their lower global warming potential, making them more environmentally friendly choices.
In addition to HFCs and natural options, other alternatives like hydrocarbon refrigerants (e.g., propane or isobutane) are gaining traction due to their efficiency and lower environmental impact. These choices reflect a growing trend toward sustainability within industrial cold room applications. Knowing what equipment is used in the cold room can further guide businesses in selecting the most suitable refrigerant for their needs.
Environmental Considerations
Environmental considerations are paramount when selecting a refrigerant for any cold room refrigeration system. Many traditional refrigerants have high global warming potentials that contribute significantly to climate change when leaked into the atmosphere. As such, regulations around these substances are becoming stricter, prompting industries to seek out greener alternatives that comply with new standards.
The shift towards eco-friendly options not only helps businesses meet compliance requirements but also enhances their reputation as environmentally responsible entities. Companies using industrial cold rooms equipped with low-impact refrigerants can market themselves as leaders in sustainability while reducing their carbon footprint effectively. This consideration extends beyond just choosing the right chemical; it encompasses an entire system approach focused on energy efficiency and long-term viability.
Choosing the Right Refrigerant
Choosing the right refrigerant involves evaluating multiple factors including efficiency, cost-effectiveness, environmental impact, and compatibility with existing equipment used in the cold room refrigeration system. Businesses must consider both immediate operational needs as well as long-term sustainability goals when making this decision. Consulting industry experts or using advanced tools can streamline this process by providing insights into which options align best with specific applications.
It's also essential to stay informed about evolving regulations related to refrigeration technology since these changes may influence future decisions on which refrigerants are permissible or advisable for use within industrial settings. By prioritizing both performance and sustainability during selection processes, companies can ensure they remain competitive while contributing positively to global efforts against climate change.
In conclusion, understanding which refrigerant is used in cold rooms requires a balanced approach that considers functionality alongside environmental responsibility; this knowledge ultimately leads to better operational practices within industrial environments.
Cold Room vs. Chiller: What’s the Difference?
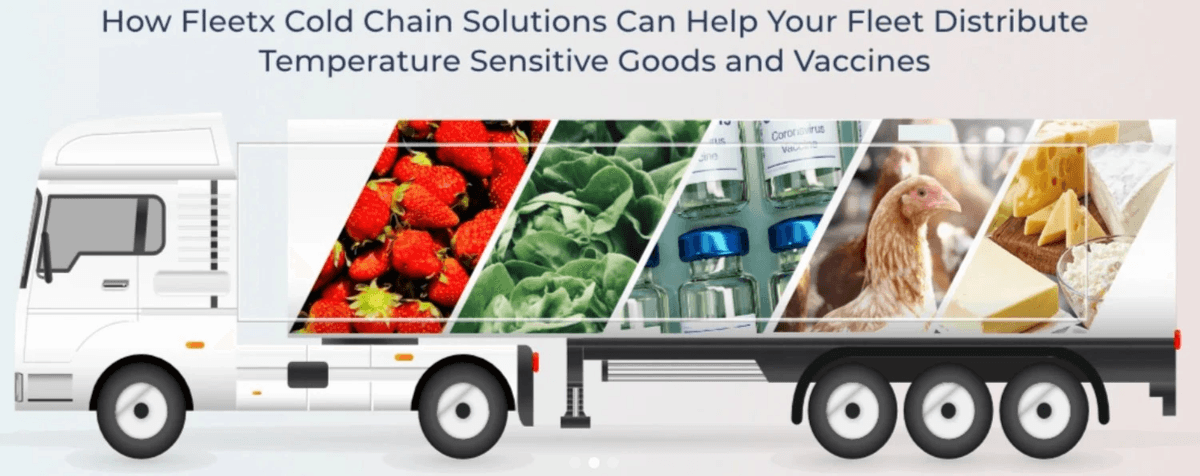
Key Distinctions in Functionality
A cold room refrigeration system is designed primarily for storing large quantities of perishable goods at consistent low temperatures over extended periods. It typically operates as a larger enclosed space with insulation to minimize temperature fluctuations, making it ideal for warehouses or distribution centers. In contrast, chillers are more versatile cooling systems used primarily for process cooling in various applications, from industrial manufacturing to air conditioning.
The functionality of these systems also differs in terms of temperature range; cold rooms usually maintain temperatures between 0°C to -18°C (32°F to 0°F), while chillers can operate at lower temperatures depending on the application requirements. Additionally, cold rooms often incorporate advanced monitoring systems to ensure optimal environmental conditions are maintained continuously. Understanding these key distinctions helps clarify which option is best suited for particular industrial needs.
Applications for Each System
Cold rooms are predominantly used in industries such as food storage, pharmaceuticals, and biotechnology where maintaining specific temperature ranges is critical for product integrity and safety. They provide an ideal environment for storing perishables like fruits, vegetables, meats, and dairy products while preventing spoilage and waste. On the other hand, chillers find their place in various sectors including HVAC systems, chemical processing plants, and even data centers where they cool machinery or fluids rather than products directly.
In summary, if your operation revolves around bulk storage of perishable items requiring long-term preservation—like an industrial cold room—you’ll benefit more from a dedicated cold room refrigeration system. However, if your needs lean towards immediate cooling solutions across different processes or spaces—such as in manufacturing or air conditioning—a chiller would be more appropriate.
Efficiency Factors
Efficiency plays a pivotal role when comparing cold rooms and chillers; both systems have unique efficiencies based on their design and intended use cases. Cold room refrigeration systems are generally designed with energy efficiency in mind due to their continuous operation over long durations; they often utilize advanced technologies like variable speed compressors that adjust according to load requirements—making them cost-effective over time.
Chillers also have efficiency ratings but can vary significantly based on operational conditions such as load demand and ambient temperature variations throughout the year. The choice between these two solutions should therefore consider not just upfront costs but also long-term energy consumption patterns; investing in high-quality equipment like Arctic Active Cooling's Top-Mounted Monoblock Refrigeration Unit can enhance performance while minimizing operational expenses.
In conclusion, understanding what equipment is used in the cold room versus chillers—and knowing what is the standard for a cold room—can greatly influence decision-making within an organization looking to optimize its cooling solutions effectively.
Essential Equipment Used in Cold Rooms
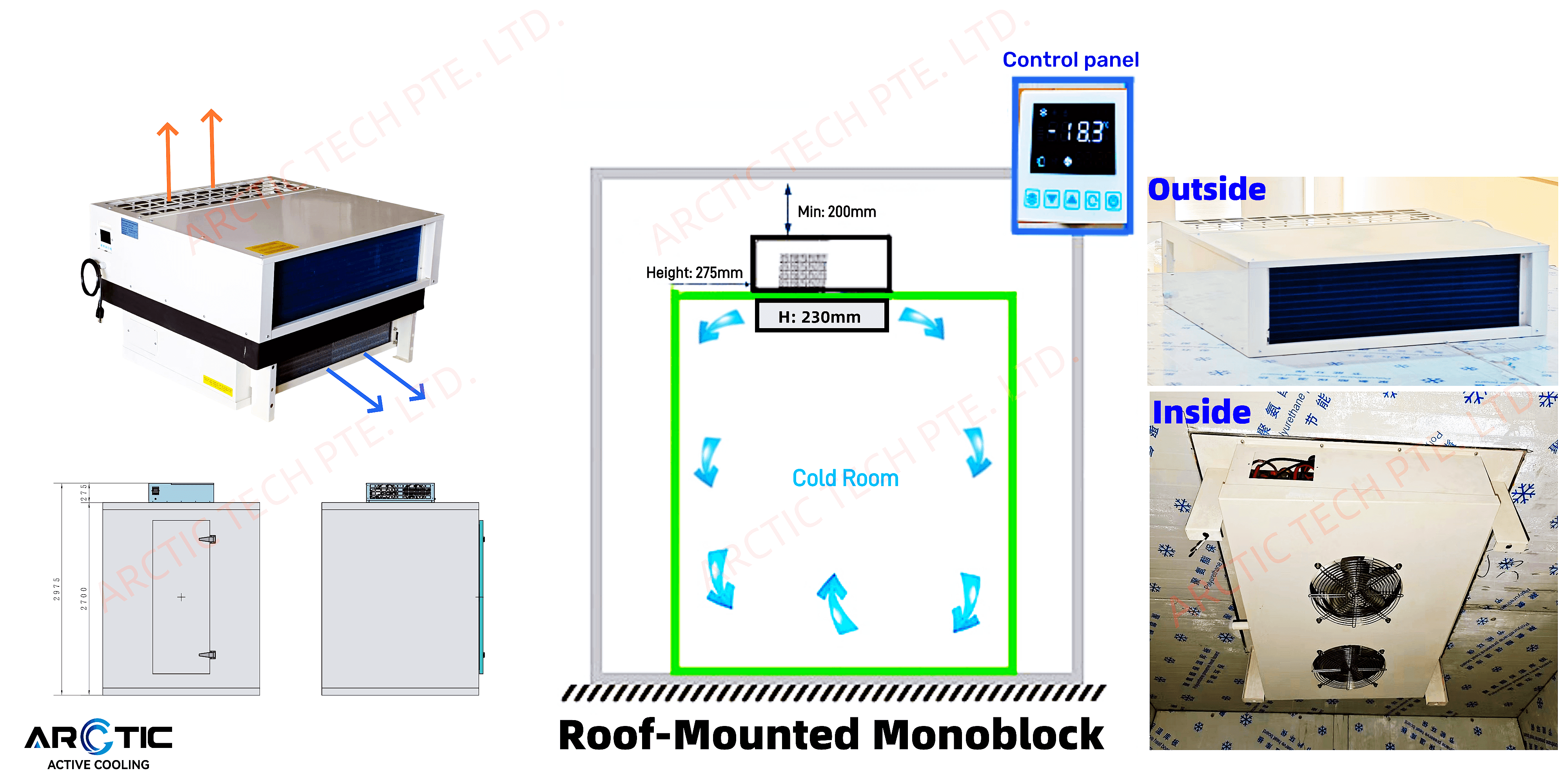
When it comes to cold room refrigeration systems, the efficiency and reliability of the equipment are paramount. A well-designed cold room relies on a combination of advanced technology and essential components to maintain optimal temperatures for various industrial applications. Understanding the equipment used in these systems is crucial for ensuring compliance with standards and maximizing performance.
Overview of Coldroom Refrigeration Systems
Coldroom refrigeration systems are engineered to provide precise temperature control, making them indispensable in industries such as food storage, pharmaceuticals, and logistics. These systems typically consist of insulated panels, refrigeration units, and monitoring devices that work together to create a stable environment. The choice of equipment can significantly influence energy efficiency, operational costs, and overall effectiveness in maintaining the required conditions.
Arctic Active Cooling Top-Mounted Monoblock Refrigeration Unit
For those seeking an efficient solution for their industrial cold room needs, look no further than Arctic Active Cooling’s Top-Mounted Monoblock Refrigeration Unit. This all-in-one system is not only compact but also powerful enough to handle the demands of commercial refrigerators and small to mid-sized cold rooms with ease. Engineered for modern cooling applications, this unit offers unparalleled efficiency and reliability while ensuring sustainability—a key factor in today's environmentally conscious market.
Supporting Equipment for Optimal Performance
To ensure that a cold room refrigeration system operates at peak performance, additional supporting equipment is essential. This includes temperature monitoring devices that provide real-time data on internal conditions as well as backup generators that maintain functionality during power outages. Additionally, proper insulation materials play a critical role in minimizing energy loss—keeping your industrial cold room efficient while adhering to standards set forth by regulatory bodies.
Standards and Regulations for Cold Rooms
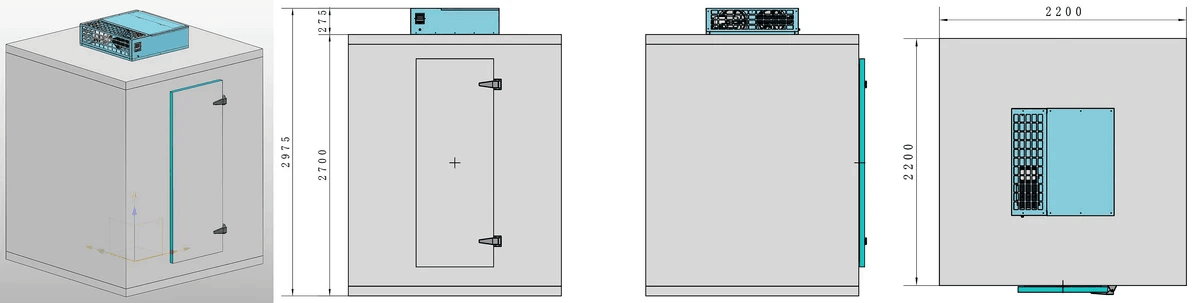
When it comes to cold room refrigeration systems, understanding the standards and regulations is crucial for ensuring safety, efficiency, and compliance. Different industries have specific guidelines that dictate how cold rooms should be constructed, maintained, and operated. Familiarity with these standards not only helps in meeting legal requirements but also enhances operational effectiveness.
Understanding Cold Room Standards
Cold room standards are established to ensure that refrigeration systems operate within safe and efficient parameters. These standards cover various aspects such as temperature control, energy efficiency, and structural integrity of the cold room itself. For instance, organizations like the International Institute of Refrigeration (IIR) provide guidelines on acceptable temperature ranges for different types of stored products in industrial cold rooms.
Moreover, these standards often specify the types of refrigerants that can be used in cold room refrigeration systems. This is particularly important when considering environmental impacts and safety measures associated with refrigerant leakage or mishandling. Adhering to these guidelines ensures that businesses maintain a high level of quality control while safeguarding public health.
Compliance Requirements
Compliance with cold room regulations involves more than just understanding the applicable standards; it requires implementing them effectively within your facility. Businesses must ensure that their cold rooms meet local building codes and health regulations related to food storage or pharmaceuticals, depending on their industry focus. Regular inspections by regulatory bodies are often necessary to confirm compliance.
In addition to construction codes, businesses must also pay attention to equipment certifications for items like compressors or cooling units used in their cold room refrigeration systems. For example, using equipment from reputable brands such as Arctic Active Cooling can help meet these compliance requirements while ensuring optimal performance in commercial applications. Failure to comply can lead to costly fines or even shutdowns.
Best Practices for Operation
To maintain an effective industrial cold room & equipment setup, adhering to best practices is essential for long-term success. Regular maintenance schedules should be established for all components of the cold room refrigeration system—this includes checking refrigerant levels, inspecting seals on doors and panels, and ensuring proper airflow around cooling units like Arctic Active Cooling’s Top-Mounted Monoblock Refrigeration Unit.
Staff training is another critical aspect; employees should understand how to operate equipment safely while recognizing signs of malfunction or inefficiency in the system. Implementing a monitoring system can also help track temperatures consistently within the cold room; this allows quick responses if conditions deviate from required levels—ultimately protecting stored goods from spoilage.
By following established standards and best practices for operation in your industrial facility's cold rooms, you not only enhance efficiency but also contribute positively toward sustainability efforts within your industry.
Conclusion
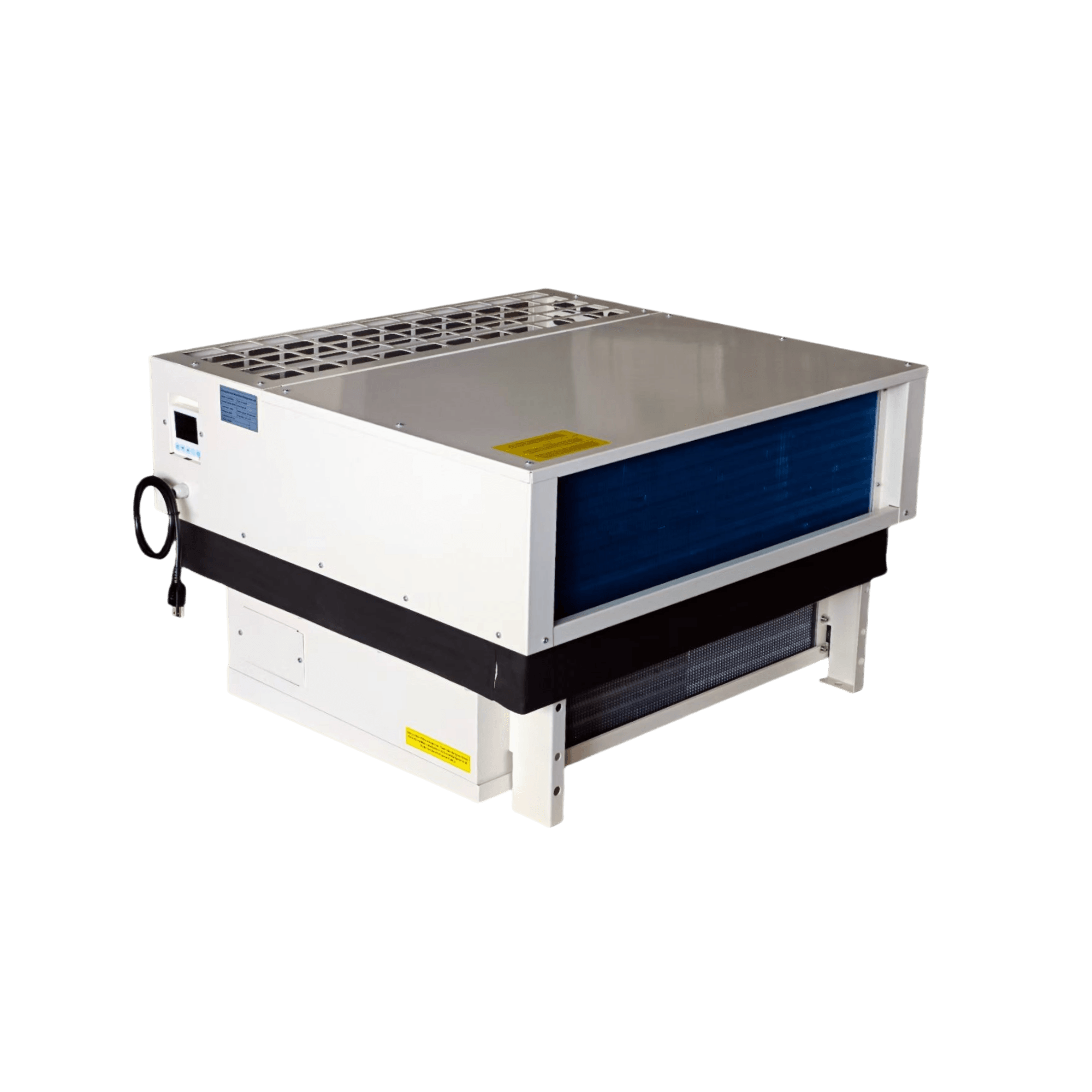
In the realm of industrial operations, cold room refrigeration systems play a crucial role in maintaining product quality and safety. These systems are not just about keeping things cold; they are essential for preserving perishable goods, pharmaceuticals, and sensitive materials. Understanding the intricacies of cold room technology is vital for industries that rely on efficient temperature control.
Why Cold Room Refrigeration Matters
Cold room refrigeration systems ensure that products remain at optimal temperatures, preventing spoilage and extending shelf life. This is particularly important in sectors like food processing and pharmaceuticals, where even minor temperature fluctuations can lead to significant losses. Additionally, with increased regulations surrounding food safety and product integrity, having reliable cold storage solutions is more critical than ever.
Future Trends in Cold Room Technology
As industries evolve, so do the technologies associated with cold rooms. Innovations such as smart monitoring systems and energy-efficient refrigerants are paving the way for more sustainable practices within the sector. Furthermore, advancements like Arctic Active Cooling’s Top-Mounted Monoblock Refrigeration Unit highlight a shift towards all-in-one solutions that enhance performance while reducing environmental impact.
Final Thoughts on Industrial Cold Rooms
In conclusion, understanding what equipment is used in the cold room and which refrigerant is used in cold rooms can significantly impact operational efficiency and compliance with standards for a cold room. The difference between a cold room and a chiller lies primarily in their functionality and application scope—both play vital roles but cater to different needs within industrial settings. As we look to the future of industrial cold rooms and equipment, embracing innovation will be key to meeting both market demands and sustainability goals.