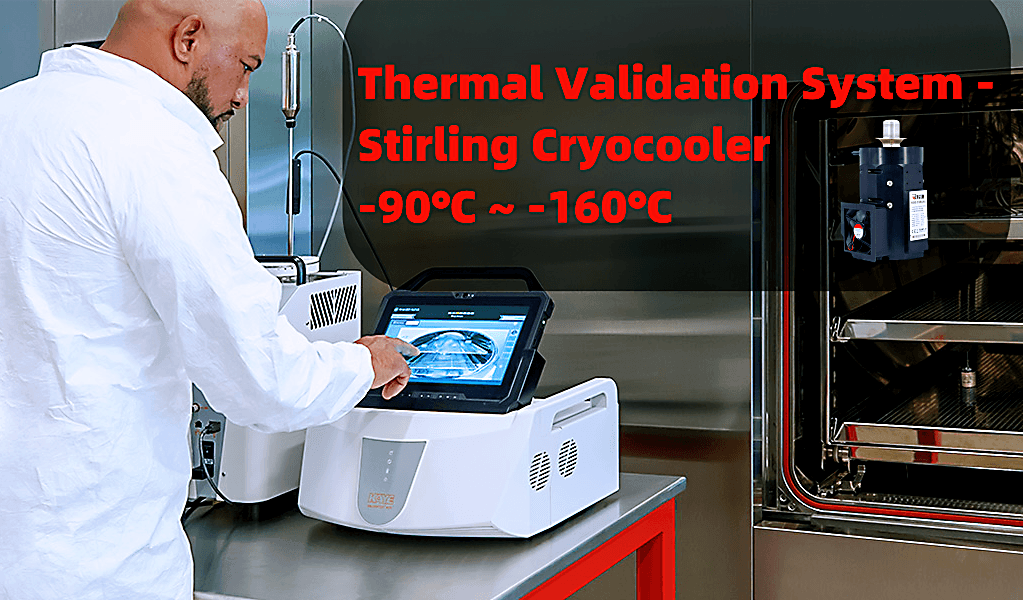
Project: Thermal Validation System Cooling
Cooling Approach: Green Power – Stirling Cryocoolera
Demand: Kaye Advanced Sensors, an innovator in advanced sensing and embedded measurement solutions for regulatory and industry-driven applications, requires a reliable, noise-free cooling system. The system must cool from 25°C to -90°C in 90 minutes and heat to 140°C in 60 minutes, addressing issues with previous compressor systems that failed to achieve precise temperatures and had start-up and noise problems. They seek RIGID’s RS100 Stirling Cryocooler with a custom metal block for integration into their calibration tank system.
Recommended products: Cryocooler RS100
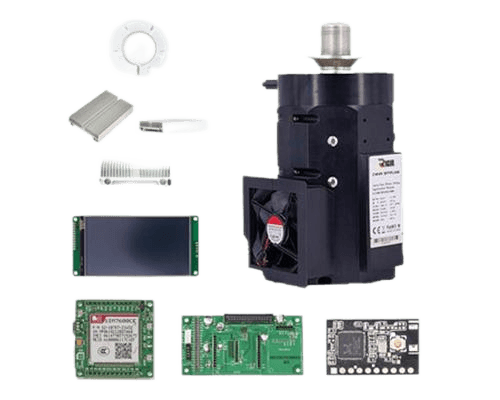
Background
In thermal validation systems, precise temperature control is crucial, especially in pharmaceutical and biotechnology industries. Traditional cooling methods, like compressor-based systems, often face challenges such as inaccurate temperature control, unreliable start-up, and excessive noise and vibration at low temperatures.
Kaye Advanced Sensors, a leader in advanced sensing technologies and measurement solutions for regulatory and industry applications, requires a cooling system that can efficiently cool from 25°C to -90°C in 90 minutes and heat to 140°C in 60 minutes. Their previous compressor systems failed to meet these needs, prompting them to seek a more reliable solution.
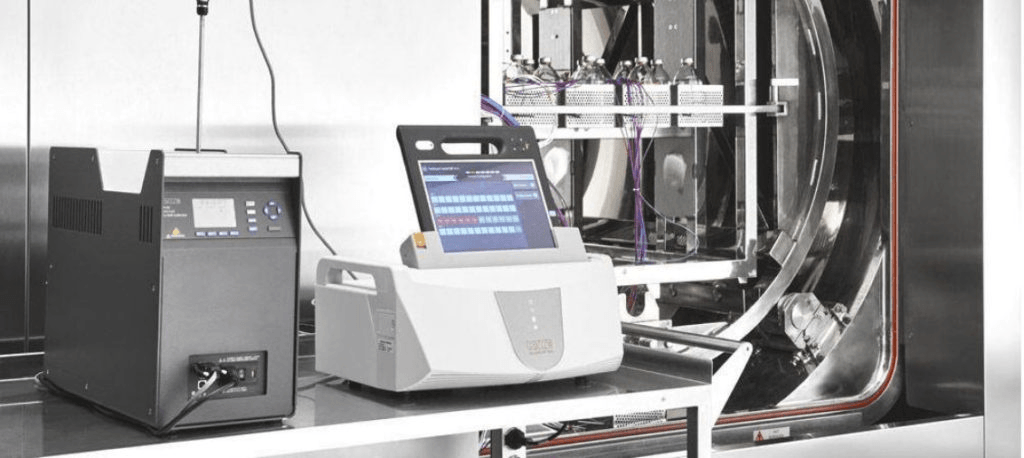
ARCTIC’s RS100 Stirling Cryocooler offers a precise, noise-free, and continuous operation cooling solution. The Stirling cryocooler excels in providing accurate and stable low temperatures, making it ideal for Kaye’s stringent thermal validation requirements. Its ability to maintain consistent performance without the start-up issues and noise associated with compressors ensures reliable validation of critical processes.
By integrating the RS100 with a custom-designed metal block for optimal thermal transfer, Kaye can enhance their thermal validation systems, ensuring compliance with regulatory standards and improving real-time decision-making.
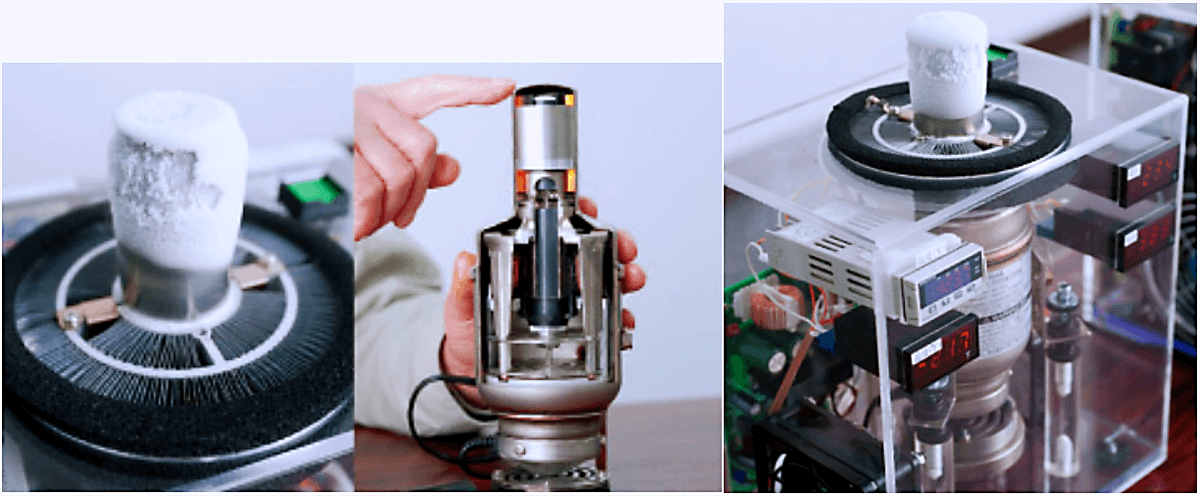
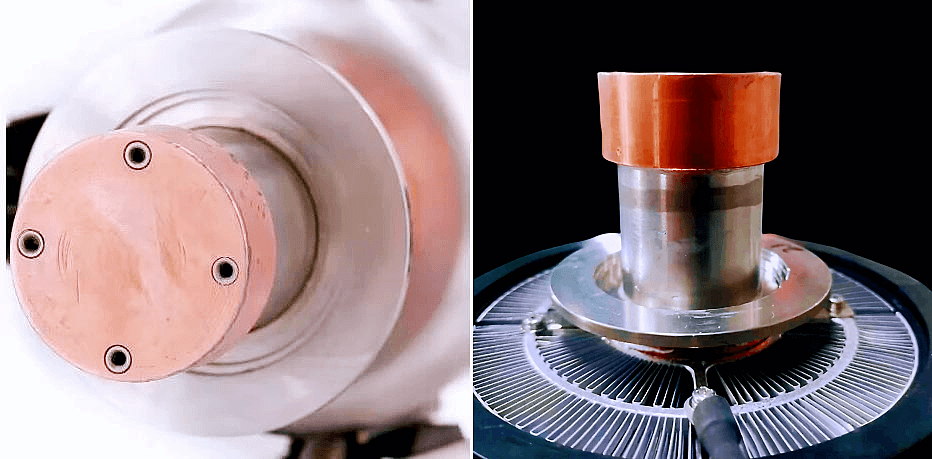
What’s Thermal Validation System?
A thermal validation system ensures precise temperature control for critical processes in industries like pharmaceuticals, biotechnology, and food processing. It involves temperature sensors, data loggers, calibration equipment, and software to monitor, validate, and document temperature data, ensuring regulatory compliance, product quality, and process efficiency. It’s crucial for maintaining safety and meeting industry standards.
How Does Stirling Cryocooler Work in Thermal Validation System?
A Stirling cryocooler is a type of cryogenic cooling system that uses the Stirling cycle to achieve very low temperatures. It is commonly used in thermal validation systems, particularly when precise and stable low temperatures are required. Here’s how a Stirling cryocooler works and its role in thermal validation systems:Working Principle of a Stirling Cryocooler
- Stirling Cycle: The Stirling cryocooler operates based on the Stirling cycle, which consists of two isothermal processes and two isochoric (constant volume) processes. The cycle includes:
- Isothermal Compression: A working gas (usually helium) is compressed in a cylinder, releasing heat to the surroundings.
- Isochoric Cooling: The compressed gas passes through a regenerator, which absorbs some of the heat from the gas.
- Isothermal Expansion: The gas expands in a second cylinder, absorbing heat from the surroundings, which produces the cooling effect.
- Isochoric Heating: The gas passes back through the regenerator, where it absorbs the previously stored heat, and the cycle repeats.
- Components: A typical Stirling cryocooler consists of:
- Compressor: Compresses the working gas.
- Regenerator: A heat exchanger that temporarily stores heat.
- Displacer: Moves the gas between the hot and cold ends of the cryocooler.
- Heat Exchangers: Facilitate heat exchange at the hot and cold ends.
- Closed System: The system is sealed and the working gas circulates continuously within the closed loop.
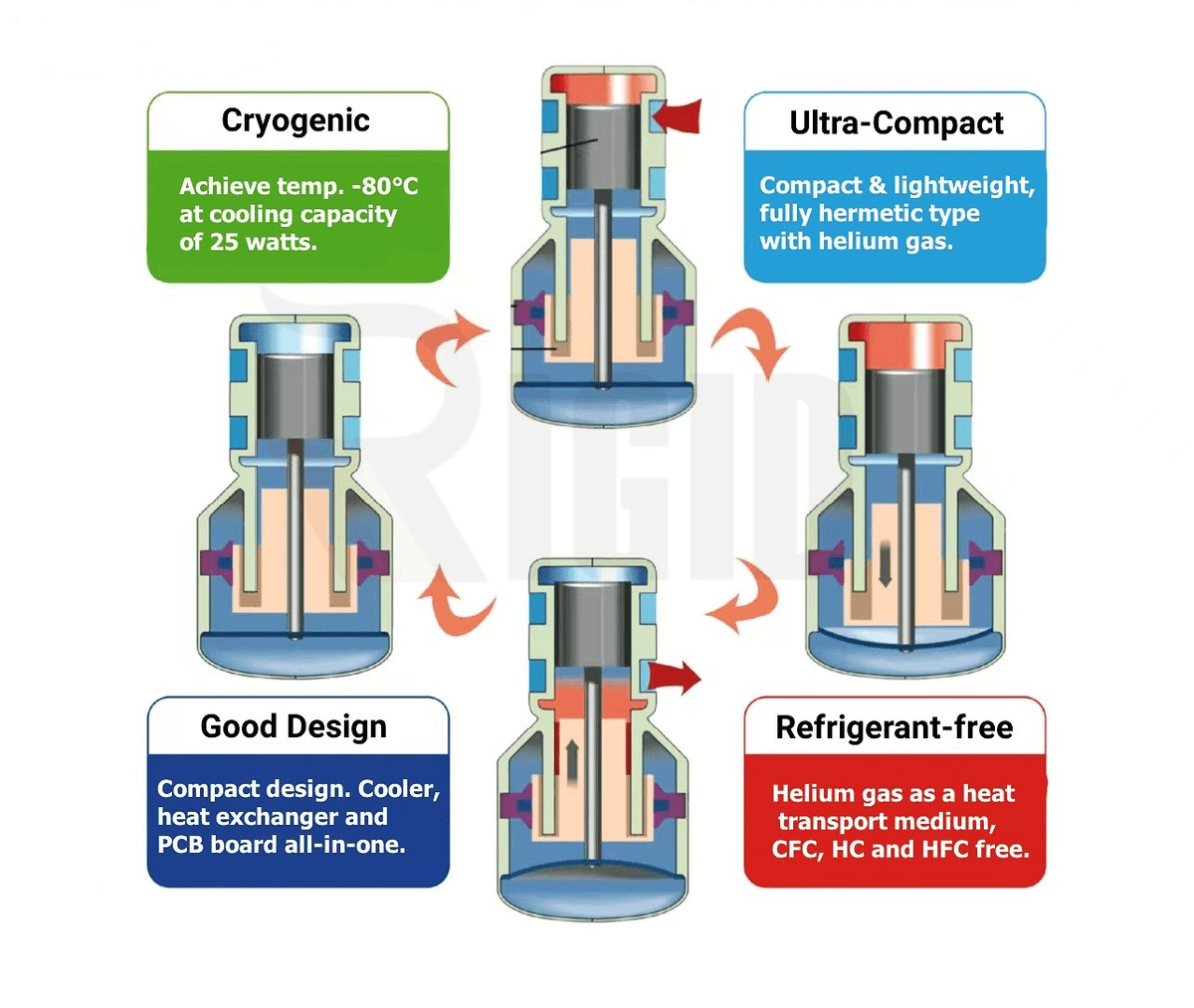
Stirling Cryocooler Working Principle
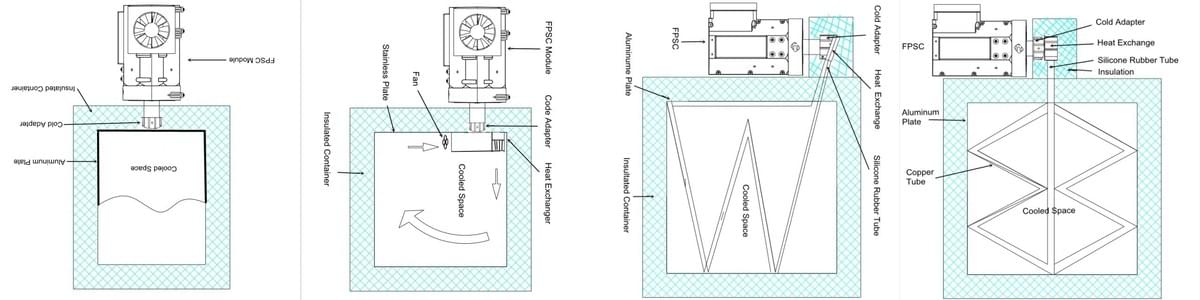
Thermal validation systems are used to ensure that various processes and equipment maintain specific temperature conditions, often crucial in industries like pharmaceuticals, biotechnology, and aerospace. Stirling cryocoolers are used in these systems for several reasons:
- Precision and Stability: Stirling cryocoolers provide very precise and stable temperatures, essential for accurate thermal validation. They can maintain temperatures within a narrow range, ensuring reliable validation results.
- Low Temperatures: These cryocoolers can achieve extremely low temperatures (down to -150°C or lower), which are often required in cryogenic validation processes.
- Compact and Efficient: Stirling cryocoolers are relatively compact and energy-efficient compared to other cryogenic cooling methods, making them suitable for various industrial applications.
- Reliability: The Stirling cycle is known for its reliability and long operational life, which is crucial for continuous and long-term thermal validation processes.
- Environmental Control: By providing a stable low-temperature environment, Stirling cryocoolers help in validating the thermal performance of equipment and processes that operate under cryogenic conditions.
In a thermal validation system, the Stirling cryocooler is typically integrated as follows:
- Setup: The cryocooler is connected to the chamber or apparatus where temperature validation is to be performed.
- Calibration: The system is calibrated to ensure accurate temperature readings and control.
- Validation Process: The cryocooler is used to bring the temperature of the chamber or equipment to the required low temperature. Sensors and data loggers monitor the temperature to ensure it remains within the specified range.
- Data Collection: Temperature data is collected over a period to validate the performance of the equipment or process under test.
- Analysis and Reporting: The collected data is analyzed to confirm that the system meets the required thermal specifications.
In summary, a Stirling cryocooler is a crucial component in thermal validation systems for achieving and maintaining precise low temperatures, ensuring the reliability and accuracy of thermal validation processes in various industries.
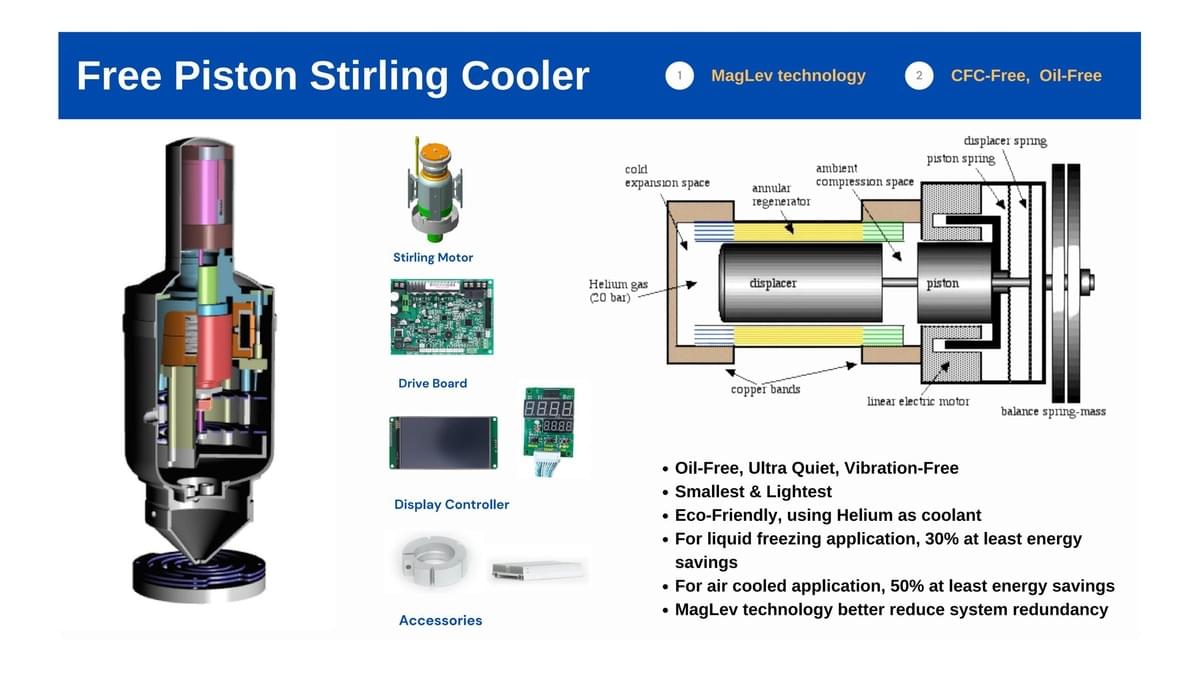
Stirling Cryocooler-RS100 Working Video
Solution
100W STIRLING CRYOCOOLER
- Model: RS100
- Input power: 24V DC
- Working current: 6A
- Noise: ≤48dB
- External Size: 132×132x336mm (LxWxH)
- Temp Range in Cold Fin (Cold part): -150℃~ 0℃

Cryocooler Features and Benefits
- High Precision Cooling:
- Provides accurate and stable temperature control from 25°C to -90°C.
- Rapid Cooling and Heating:
- Achieves target temperatures quickly, cooling within 90 minutes and heating up to 140°C in 60 minutes.
- Continuous Operation:
- Designed for uninterrupted, reliable performance.
- Low Noise and Vibration:
- Operates quietly, reducing noise pollution and minimizing vibration issues.
- Compact and Efficient Design:
- Space-saving and energy-efficient, ideal for various industrial applications.Benefits of Thermal Validation System
- Improved Accuracy:
- Ensures precise temperature control, critical for validating thermal processes.
- Enhanced Reliability:
- Continuous operation without the start-up and noise issues associated with compressors.
- Regulatory Compliance:
- Meets stringent regulatory standards, ensuring product safety and quality.
- Increased Efficiency:
- Rapid temperature changes improve process efficiency and reduce downtime.
- User-Friendly Integration:
- Easily integrates with existing systems, simplifying the setup and operation.
Advantages of Cryocoolers in Thermal Validation Systems
ARCTIC Stirling cryocoolers provide high precision and stability, ensuring accurate temperature control crucial for thermal validation. They achieve rapid cooling and heating, reaching target temperatures quickly to enhance process efficiency and reduce downtime.
Unlike compressor-based systems, Stirling cryocoolers offer continuous, reliable operation without frequent start-up issues, and operate with low noise and minimal vibration, creating a quieter and more stable working environment.
Energy-efficient and compact, Stirling cryocoolers reduce operational costs and save space, making them easy to integrate into existing setups. They are more reliable and require less maintenance compared to traditional compressor systems, resulting in higher system uptime and longevity.
Additionally, Stirling cryocoolers ensure compliance with stringent regulatory standards, essential for industries like pharmaceuticals and biotechnology.
In comparison, compressor cooling systems often face challenges such as inaccurate temperature control, noise, vibration issues, and higher energy consumption, making Stirling cryocoolers a superior choice for critical temperature control applications.